OUR Process: Keeping with the Spirit of Stuttgart
We believe building German classics the right way is the only way.
The placement of a Banyan badge is the final step in a months-long process that takes thousands of man-hours and involves no less than five different teams of highly skilled craftsmen. Sure, we could restore a car faster and cheaper, but then it wouldn’t be a Banyan.
PROCUREMENT: THE DONOR VEHICLE
The first step is identifying a suitable car to become the next Banyan German Classic. Even though our proprietary process involves restoring every single nut and bolt, we still have exacting criteria for the cars we choose to begin with. We look for examples that are as accident-free and original as possible, with signs that they’ve been well looked after. For our 230 GE builds, we get them straight from the Swiss Army, whose neutral stance means they haven’t seen combat, and whose legendary discipline means they’ve been meticulously maintained.
The only exception to this is for the customers who have asked us to electrify classic Porsche 911s. We can’t bring ourselves to deface the drivetrain of an original 911, so for those builds, we seek out donor cars that need saving - you know those 911s with wild body kits that look like a cocaine-fueled fever dream and Corvette engine conversions? Those are the ones we bring back to the city where they were born to give them a second chance at once again being timeless.






BODY WORK
The individual body panels are delivered to Stuttgart’s finest bodyworkers. This is the go-to shop for multi-million dollar, concours-winning restorations, and that process is the same one all Banyan German Classics receive. Every metal bit is baked for hours at extremely high heat to separate any impurities and then dipped in a chemical peel to return the metal to its bare state. It’s then subject to a second bath to remove any traces of the chemical peel and coated in a zinc phosphate solution to ensure that the anti-corrosive solution applied next achieves maximum adhesion.
All panels are then “e-coated”- a process that involves submerging them in an electrophoretic bath that has been positively charged, which allows every single element - including the internal layers - to receive an even coating, providing superior smoothness, better protection from rust, and none of the loss in strength or structure as experienced with traditional blasting methods. To our knowledge, Banyan is the only producer of restored vintage utility vehicles that uses this electrophoretic coating as a standard part of our process.






PERFORMANCE, ASSEMBLY & TUNING
Once the right car has been acquired, it’s brought to our expert builders, who have been specializing in further improving brilliant German cars for 95 years. They give every car a thorough mechanical and physical inspection and catalog everything it could possibly need, and then they get to work completely disassembling it.
The engines are sent straight to a team led by an AMG master tech with more than 35 years of experience, where he was responsible for the engine work on iconic creations such as the original “Red Pig”. Utilizing only period-correct tuning techniques, each engine is meticulously rebuilt for optimum power and reliability. In the case of our 230 GE builds, the original 2.3-liter engine - the same block used in the 190 EVO - is rebored to 2.8 liters as standard, improving its power output from 125hp to 250hp.
Suspension components, brakes, and transmissions are completely rebuilt using only parts manufactured by suppliers that Porsche and Mercedes-Benz use directly - if it’s not good enough for them, it’s not good enough for us. The freshly painted and chromed body components are then reunited with the interiors and internals back at the workshop, where the cars are reassembled using all-new hardware. Some eight months after the process begins, a thorough series of final tests are performed to make sure everything is working perfectly, the only then is a vehicle approved to be christened a Banyan and provide its lucky new owner with an unparalleled experience in contemporary classic motoring.


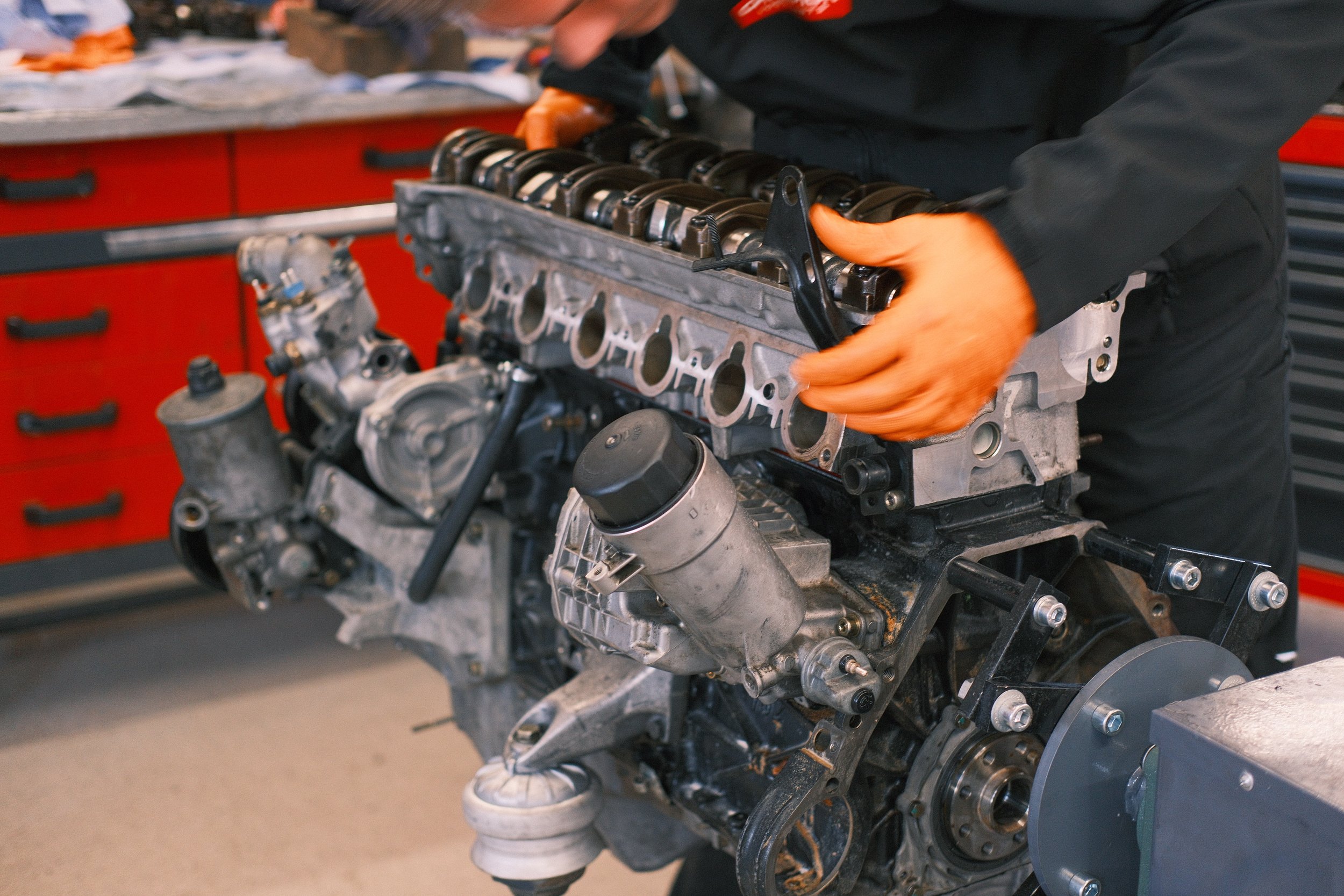



UPHOLSTERY
Our interiors are taken a few miles down the road to a small atelier which is also hired by the Porsche and Mercedes-Benz museums to upholster the cars in their permanent collections. Brand-new leathers, vinyl, and carpeting from the original mills are hand sewn onto repolished frames. Wood accents are stripped, sanded, and relacquered if found to still be perfectly intact, but if there's even a single crack, every piece is replaced to ensure continuity.





